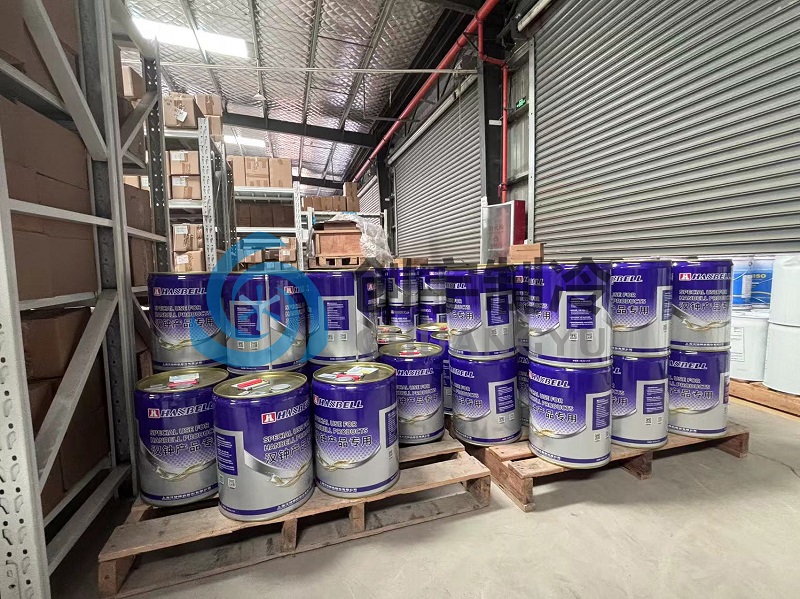
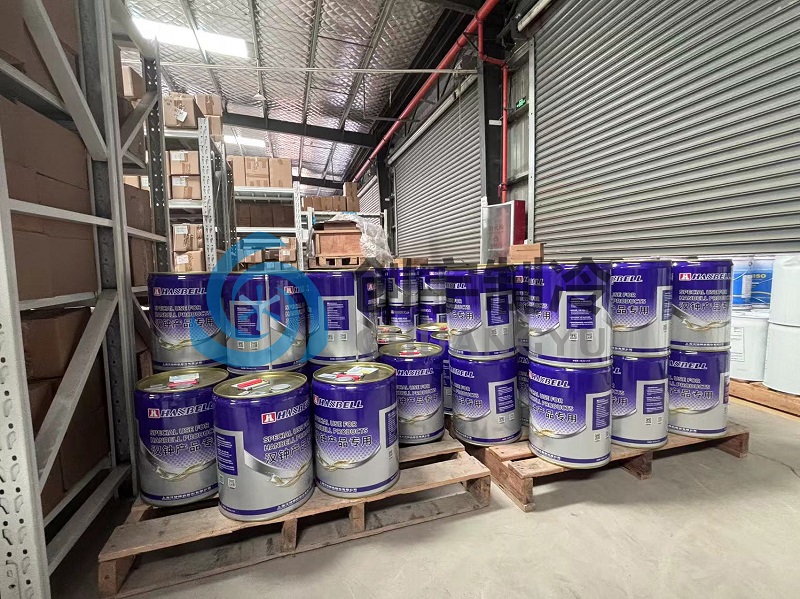

Refrigeration compressor refrigerant oil replacement standard
Refrigeration oil change indicators:Generally, the indicators for judging whether the refrigeration oil can continue to be used are: appearance, viscosity, acid value, moisture, pour point, flash point, compressive strength, copper corrosion, mechanical impurities and insolubles, etc. 01 Appearance:Whether the quality of the refrigeration oil changes or not should be determined through certain chemical and physical […]
Refrigeration oil change indicators:
Generally, the indicators for judging whether the refrigeration oil can continue to be used are: appearance, viscosity, acid value, moisture, pour point, flash point, compressive strength, copper corrosion, mechanical impurities and insolubles, etc.
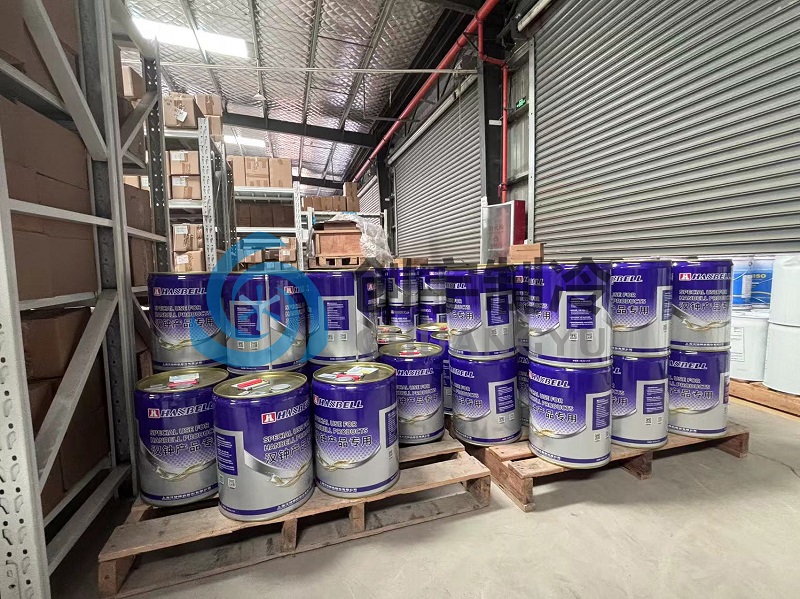
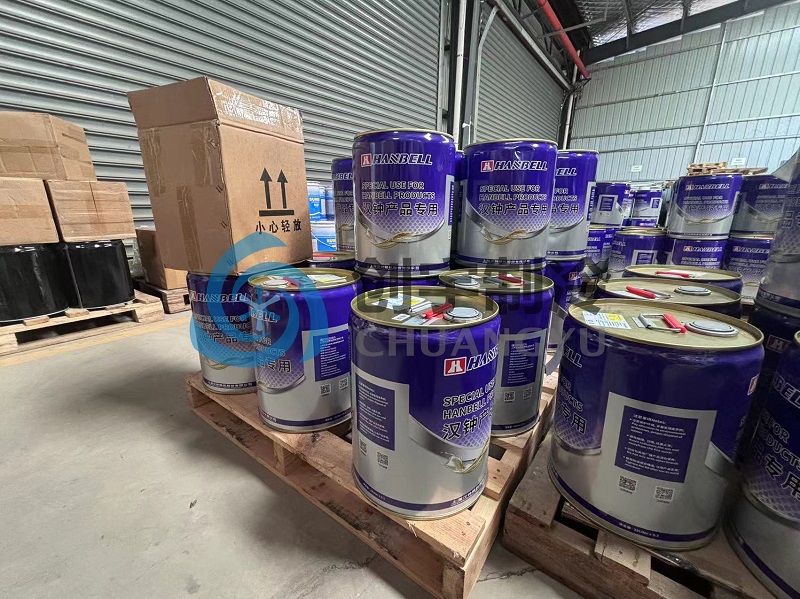
01 Appearance:
Whether the quality of the refrigeration oil changes or not should be determined through certain chemical and physical analysis. In normal use, the quality of the oil can also be intuitively judged from the appearance color of the oil. High-quality refrigeration oil should be colorless and transparent. After a period of use, it will turn light yellow. As the use time increases, the color of the oil will gradually darken and the transparency will deteriorate. If the refrigeration oil turns orange or reddish brown, it should be replaced.
02 Viscosity:
The kinematic viscosity value of the refrigeration oil is the main indicator reflecting the lubrication performance of the oil, and it is also the basis for many countries in the world to formulate refrigeration oil grades. Too high viscosity not only cannot guarantee the low-temperature performance of the oil, is not conducive to heat transfer, but also reduces the power of the machine; too low viscosity will not form the proper oil film at the friction part, resulting in increased equipment wear and even “cylinder pulling” and “sticking” and other faults.
03 Acid value:
Acid value is an important indicator of refrigeration oil, and its corresponding test method is GB/T4945 or GB/T7304. The size of the acid value in refrigeration oil reflects the refining depth and oxidation degree of the oil to a certain extent.
04 Water content:
In the refrigeration cycle system, even if there is only a small amount of water, ice plugging will occur at the low-temperature throttling device and cause the refrigeration oil to produce floccules prematurely. At high temperatures, water content will also reduce the stability of the oil. On the other hand, the closed refrigeration oil is in direct contact with the motor coil, and the presence of water will damage the insulation and even cause motor breakdown accidents.
05 Pour point:
The lowest temperature at which the oil can flow is called the pour point of the oil. When the refrigerant is compressed, some oil mist often enters the pipeline. Even if it passes through the oil-gas separator, the two cannot be separated cleanly. This requires the oil to have good low-temperature fluidity (low pour point) in the refrigeration system to avoid blocking the throttling part to stop the chiller from working or attaching to the evaporator heat exchange tube to reduce the heat transfer efficiency.
06 Flash point:
The flash point of refrigeration oil refers to the lowest temperature at which flash fire occurs when the oil vapor generated during heating mixes with air and contacts a flame. If the flash point of refrigeration oil decreases, it means that light oil is mixed in the oil or some of the oil has decomposed to form low-boiling decomposition products. Generally speaking, the flash point of refrigeration oil is 15-30℃ higher than the compressor discharge temperature.
07 Compressive strength:
Compressive strength is also called breakdown voltage or dielectric strength. It means that when the voltage is gradually increased to a certain value when the refrigeration oil is placed in a container with an electrode and a voltage is applied, the resistance of the oil suddenly drops to zero, and a strong current passes through the oil in the form of sparks or arcs. The critical voltage value at this time is called dielectric strength. The main factors affecting the breakdown voltage of refrigeration oil are moisture, impurities, temperature, etc.
08 Copper sheet corrosion:
The copper sheet corrosion test is currently the most important method for determining the corrosion of industrial lubricants. It is a test of the tendency of oil products to corrode metal surfaces in contact under specified conditions. The corrosion resistance of oil products can reflect the refining depth and deterioration degree of oil products to a certain extent.
09 Mechanical impurities and insoluble matter:
Mechanical impurities are one of the routine monitoring items for the lubrication management of chiller compressors, because mechanical impurities in oil products will accelerate the abnormal wear of compressors, and will also block the oil circuit and filter, causing lubrication failure of the compressor. Mechanical impurities are one of the indicators for judging whether refrigeration oil needs to be changed. Usually, mechanical impurities below 0.005% are considered to be free of mechanical impurities. If it exceeds 0.005%, it contains mechanical impurities and the refrigeration oil is judged to be unqualified.